Rocket Factory Augsburg Discusses SaxaVord Benefits
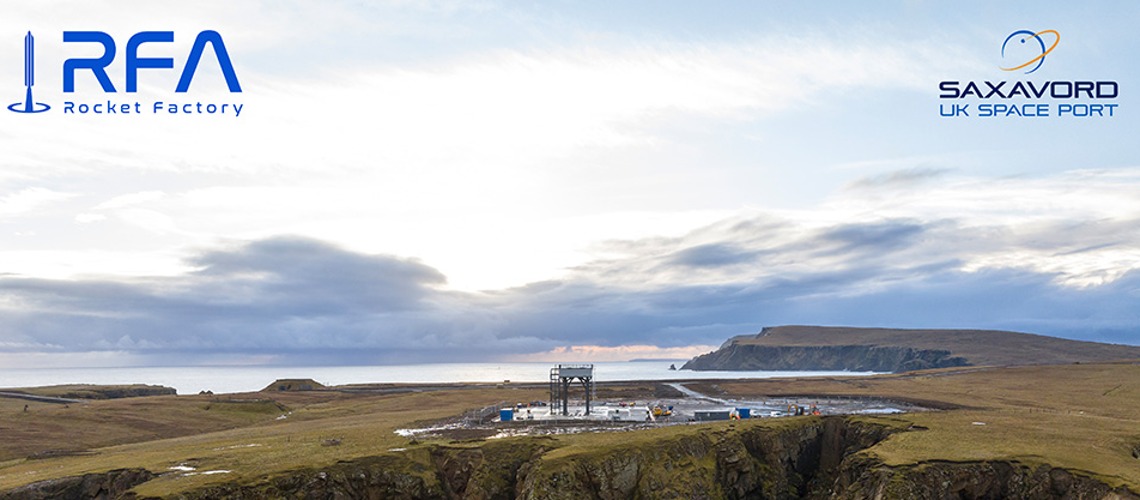
Rocket Factory Augsburg explored the Benefits of SaxaVord Spaceport. They say:
"Reaching the launch pad is a monumental milestone for any rocket company, but building the launch pad is an entirely different challenge. It’s essential for launching a rocket, yet it often remains an unsung hero in the background. At Rocket Factory Augsburg (RFA), we’re dedicated to sharing the story of our “Stage Zero” and giving you a behind-the-scenes look at our process.
While most people focus on the rocket itself (which is completely fair), we delve deeper into the question: “But how do we make it actually happen?” The entire process is incredibly complex and requires meticulous planning. Our launch pad must store, amongst others, approx. 40,000L of fuel, 125,000L of LOx, 125,000L of Nitrogen and 5,000L of Helium. It then has to fill our three rocket stages at precise temperatures, to a specific time, provide power to all systems and sensors, and protect itself from the immense power of our nine 500,000HP Helix engines roaring to life.
Why SaxaVord? The Strategic Location of Our Stage Zero
Choosing SaxaVord Spaceport as the base for our flight operations was a decision made after careful consideration of various factors: Firstly, SaxaVord and RFA are both private companies who share the same approach of cost-efficiency, a fast pace and “go-get-it”-mentality. Secondly, Shetland has a rich oil and fishing industry with existing infrastructure (e.g. industrial harbors, tool stores, suppliers). Finally, it is perfectly located for launches into polar low earth orbits.
While launching from the equator provides additional speed from the Earth’s rotation, this advantage is primarily relevant for higher or further orbits (e.g., GEO, Lunar, or interplanetary). For our purposes, proximity to the equator is not a crucial factor since we will be launching in a direct north/south direction. We’re primarily targeting polar and sun-synchronous orbits as that is the optimal location for the more commercially interesting constellations and Earth Observation (EO) satellites.
Now, as we set the scene in Scotland, building a rocket launch pad involves much more than just concrete and steel.
Our team of engineers has worked tirelessly to design and implement the technical infrastructure needed to support our rockets. From fueling systems to communication with, and erection of the RFA ONE, every detail has been carefully planned to make sure we have a safe, efficient, and successful launch. Let´s have a look at some of the main elements:
Key Components of Our Launch Site
- Launch Stool Structure: You know what it looks like. A large, gray steel structure on four legs, to put it simply. But the launch stool does not just hold our approx. 60 metric ton RFA ONE in place before launch. It also allows us to work on things like the engines when the vehicle is fully integrated and vertical. The structure is made of stainless steel and has to withstand the strong winds and salty (corrosive) sea air. Inside we have huge water tanks for our water deluge system, but we’ll share more on that later. By the way: The company that built the launch stool for us comes from the maritime structural engineering sector. We want to go beyond highly specialized (and correspondingly paid) aerospace suppliers – not only for RFA ONE but everywhere.
- Fuel Farm: Our so-called fuel farm is where we store everything we need to fuel our launch vehicle. Inert gases, propellants, oxidizers and other liquids are all kept here until it’s time to fill RFA ONE with them in a precisely timed and temperature-controlled manner. For example, LOX with its -183 degree Celsius boiling point gases off at an ambient temperature so we have to continuously cool it and fill it into the rocket at precisely the right temperature so that it is perfectly fueled at T-1:00. The fuel farm is protected by an earth wall and connected to the launch stool by several different sized pipelines. We have over 1,100 sensors and over 1,400 valves and regulators on that ground support equipment (GSE) ensuring everything is perfectly coordinated – keeping track of everything is crucial and an art in itself!
- Umbilical Tower: The large yellow tower is our umbilical tower. All fuel pipelines, power and data cables run up the rocket to the respective stages via this tower using interfaces. These only get disconnected when we get to lift off. If one of them gets stuck unplanned, we’ll have a problem. Further up the umbilical tower, we have collar clamps to stabilize the rocket in windy conditions. There are also eight massive hold-down clamps at the lower end. These clamps only let go when the thrust is right and all systems are running as planned. By the way, we made our umbilical tower by repurposing a decommissioned and commercially available construction site crane. Classic, cost-effective, pragmatic RFA. 😉
- AIT (Assembly, Integration, Testing) Hangar: Like the launch stool, our hangar is another seemingly simple structure: a steel building with a concrete floor. But behind the doors, it’s the place where all the magic happens! We will conduct our final tests in this hangar before integrating all three stages of RFA ONE into the final launch vehicle. The hangar serves as our technical workshop, complete with a clean room for integrating our customers’ satellites with our Redshift OTV.
- Main Control Center: This is the central hub of activities on launch day. From our MCC, the core launch team will monitor and control all systems before, during and after the test flight.
Safety Considerations
- Flame Deflector Ramp: We have constructed our own ramp that sits directly below the rocket. This serves to deflect the powerful exhaust jet of RFA ONE so it exits horizontally. Without it, the exhaust jet would go straight into the ground with nearly 700 km/h, causing dust and stones to be thrown upwards against the rocket and into the engines. While the ramp is made of stainless steel (what else), we have applied a very special and fire-resistant concrete to it to make it reusable.
- Water Deluge System: The aforementioned tanks inside the launch stool can hold approx. 90,000 liters of water. Just before those nine powerful Helix engines ignite, we inject the water into the sides of the exhausts. This reduces the heat from flames and dampens noise and shock waves, maintaining the structural integrity of the stool and protecting the vehicle. This is also what creates the large white cloud you usually see during rocket launches – it’s just water vapor.
- Lightning Protection: The umbilical tower is also the highest point on the entire SaxaVord peninsula. So we have installed a lightning conductor, just in case – better to be safe than sorry!
- Communication Systems: The most important safety consideration when on our launch site, especially so when the stages are on the launch pad and we are testing. It is essential to communicate with both the rocket and each other continuously. We have to ask questions like: Is the pressure right? How much fuel do we have in the tank? Are the engines cold enough? Are all the valves working? Does the flight computer have everything under control? To monitor this, we (currently) have 458 sensors on RFA ONE and over 1.100 sensors on the launch pad. They automatically check the health of all ground systems and the rocket and send the data to our team who communicate with each other via a radio system.
From Design to Assembly to Lift Off: It’s All About the Journey
The process of building Stage Zero was a journey marked by challenges and collaboration. In true RFA fashion, the design philosophy for the launch site was to aim for low-cost and standardization. We achieved this by building the site from the ground up and designing all our systems and modules to fit into standard shipping containers. It made it easy to transport everything from Augsburg to Shetland and beyond. Our launch site can be packed down and put up anywhere in the world, further adding to our flexible and low-cost approach.
Ultimately, designing and building Stage Zero has been a challenging but highly rewarding experience for everyone involved. Our recent first stage hot fire has shown that the systems are working well and that we can now push on with finalizing everything for our first test flight. Our hope with this blog post is to shine a little more attention on this marvel of engineering.
The rocket is one thing – what it takes to really get this thing off the ground is a story all of its own."